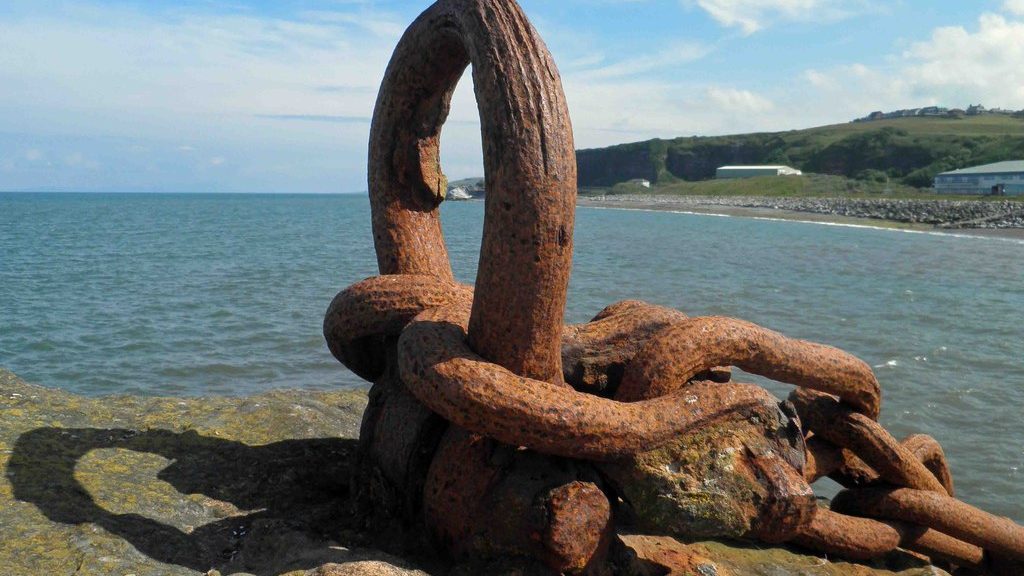
La corrosion
Alan Williams, Prof. hon. Université de Genève
Vous aurez peut-être lu que, lors de son escale à La Rochelle en juillet 2022, Gaia a subi le renouvellement de ses anodes. Que cache cette phrase un peu mystérieuse, vaguement suggestive d’une intervention chirurgicale ? Il s’agit d’une mesure contre la corrosion, phénomène que chacun connaît mais dont on parle rarement des aspects scientifiques même si nous en voyons des exemples chaque jour. L’importance économique de la corrosion n’est pas négligeable, avec des coûts estimés à quelques trois pour cent du produit brut mondial. Ce texte vise à donner une vision un peu plus large d’un phénomène omniprésent.
Commençons par rappeler certains phénomènes familiers. La corrosion est une réaction chimique subie par les métaux en contact avec l’air et l’eau. Certains métaux, dits nobles, ne semblent pas subir de changement – l’or en est un exemple. D’autres métaux, comme le cuivre dans une pièce de monnaie ou une canalisation, montrent une réaction indiquée par la perte de brillance du métal (Figure 1A), mais ne semblent pas être diminués physiquement. Enfin, d’autres métaux, dont le fer est le meilleur exemple, peuvent être complètement rongés par la corrosion (Figure 1B).
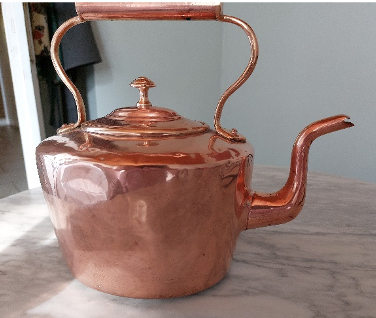
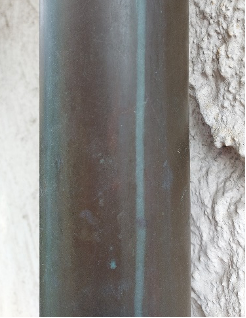
A
B
Figure 1. A – la couleur du cuivre natif (en haut) se perd lorsque celui-ci est oxydé par l’air (en bas) ; B – Corrosion du fer menant à la rupture d’un élément du pont de fer sur la rivière Nandu, province de Hainan, Chine. Source : Anna Frodesiak, CC0, via Wikimedia Commons.
Vous saurez probablement que la corrosion semble plus rapide en présence de l’eau de mer. Ceci est en grande partie dû à la présence d’ions chlorures dans l’eau et ce phénomène est aussi observé pour les automobiles dans les régions où les routes sont salées en hiver.
La corrosion est normalement assez lente, mais inévitable. La plupart des objets anciens métalliques trouvés par les archéologues ont subi la corrosion. Sur une échelle de temps géologique, presque tous les métaux sont transformés par la corrosion. Parmi les 80 éléments trouvés à la surface de la Terre, la grande majorité sont des métaux à l’état pur, mais ils ne sont que très rarement trouvés à l’état pur ou natif (sans combinaison avec d’autres éléments). Ils se trouvent généralement dans des minéraux combinés avec d’autres éléments dans des oxydes, sulfures, carbonates, silicates et bien d’autres. Dans les minéraux, les atomes métalliques sont présents sous forme de cations, c’est-à-dire d’atomes ayant perdu un ou plusieurs de leurs électrons, ces pertes étant compensées par les interactions avec les autres éléments présents dans le minéral.
L’homme découvre les métaux.
Jusqu’à la période néolithique l’homme ne connaissait que les métaux qui se trouvaient dans la nature sous forme natif : essentiellement l’or, l’argent et le cuivre avec, en Amérique du Sud, le platine. Ces métaux mous et malléables pouvaient être travaillés, notamment pour la bijouterie, mais n’étaient guère utilisables pour les outils. L’Age néolithique voyait l’homme acquérir une certaine maitrise du feu pour la production des céramiques et, grâce à cette technologie, il devenait possible d’extraire les métaux purs des minerais. Du point de vue chimique, l’extraction du métal consiste à fournir des électrons aux cations dans le minerai, retrouvant ainsi le métal natif. Une telle réaction est une réduction, la source des électrons étant typiquement le carbone sous forme de charbon de bois. Le premier métal largement utilisé était le bronze, un alliage de cuivre et d’étain, à la fois plus dur que le cuivre natif et, ayant un point de fusion inférieure à celui du cuivre pur, plus facile à couler. L’extraction se fait par le chauffage des oxydes d’étain et de cuivre mélangé avec le charbon de bois. Ainsi débutait l’âge de bronze. Il s’agit du début de la métallurgie, initiant du même coup le commerce des minerais du cuivre et de l’étain, parfois sur des distances considérables, par exemple entre les Cornouailles et le Méditerrané.
L’étape suivante fut l’extraction du fer, marquant l’âge du fer. On peut s’étonner que ceci vient après l’âge de bronze car l’oxyde de fer, minerai pour sa production, est beaucoup plus abondant que les minerais pour le cuivre et l’étain. Toutefois, le fer dans les minerais est beaucoup plus difficile à réduire que le cuivre ou l’étain et il a donc fallu améliorer les fourneaux utilisés pour la réduction pour y arriver. On voit donc qu’il est plus ou moins facile d’effectuer la réduction en métal selon l’élément. Les chimistes ont classé les métaux dans une série électrochimique, avec à une extrémité les métaux faciles à réduire (or, argent, cuivre) puis l’étain, ensuite le fer, jusqu’au plus difficiles comme le sodium ou le lithium à l’autre extrémité. Ces derniers sont souvent classés comme électropositifs. C’est seulement avec le développement des méthodes électrochimiques au 19ème siècle que les métaux électropositifs tels que le sodium, le magnésium ou l’aluminium ont pu être isolés.
D’où vient la corrosion ?
Nous avons vu que l’obtention du métal pur exige l’addition d’électrons à un cation, soit la réduction. Dès lors ce n’est pas étonnant que le métal ainsi obtenu pourrait perdre de ses électrons (une oxydation) pour se combiner avec d’autres éléments, en quelque sorte la réaction inverse de l’extraction. Les métaux électropositifs, ceux qui sont les plus difficiles à réduire, seront les plus enclins à perdre leurs électrons ou à s’oxyder. Le lithium et le sodium ne sont jamais trouvés à l’état natif dans la nature car ils réagissent très vite avec l’oxygène de l’air ou même avec de l’eau. A l’autre extrémité de la série électrochimique, l’or et la platine sont très difficiles à oxyder, et peuvent rester exposés à l’air sans attaque chimique.
Toutefois, la série électrochimique n’explique pas tout. Nous sommes entourés d’objets en métal qui ne semblent pas subir de corrosion alors que, selon la série électrochimique, ils devraient réagir avec l’oxygène de l’air – l’aluminium en est un exemple. Nous devons regarder de plus près comment un objet métallique est oxydé par l’air. Ceci est montré dans la Figure 2 ci-dessous :
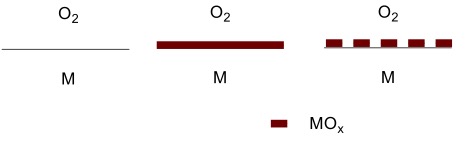
Figure 2. Gauche – le métal en contact avec l’oxygène ; centre – formation d’une couche étanche d’oxyde, la corrosion s’arrête ; droite – formation d’une couche poreuse d’oxyde, la corrosion se poursuit.
Le schéma à gauche correspond à l’air en contact avec un métal noble tel que l’or ou le platine. Il n’y a pas de réaction entre oxygène et métal. Toutefois, pour la plupart des métaux, le métal réagit avec l’oxygène pour former une couche d’oxyde. Le métal perd des électrons pour former des cations, Mn+ alors que l’oxygène les accepte pour former des anions oxyde, O2-. Les ions Mn+ et les ions O2- se combinent pour donner l’oxyde qui aura différentes compositions selon le métal (par exemple, Cu2O, PbO, Al2O3 ou TiO2) et nous l’appellerons donc simplement MOx. Le plus souvent, la couche d’oxyde est plus volumineuse que le métal et la couche couvre entièrement la surface comme montré au centre de la figure. L’oxygène et le métal ne sont plus en contact et la réaction s’arrête. Nous voyons donc la formation d’une couche protectrice. Même si la couche est rayée, une nouvelle couche se formera où le métal est en contact avec l’air. Le chrome et l’aluminium sont deux métaux qui montrent cet effet et donc ne semblent pas s’oxyder. Enfin, à droite, nous voyons le cas où l’oxyde est moins volumineux que le métal. La couche d’oxyde n’est plus étanche mais poreuse, et l’oxydation se poursuit car l’oxygène peut toujours atteindre le métal. Ceci est le cas avec le magnésium ou le sodium. Avec le temps, un ruban de magnésium métallique se transforme en poudre d’oxyde de magnésium.
L’eau intervient -la rouille
La plupart des métaux ne réagissent pas avec l’eau (parmi les exceptions se trouve le lithium, ce qui explique pourquoi il est difficile d’éteindre l’incendie d’une batterie de lithium) mais la corrosion est souvent accélérée par la présence d’eau. En effet, l’eau peut attaquer et dissoudre la couche protectrice d’oxyde permettant ainsi à la corrosion de reprendre. L’effet est plus marqué si l’eau contient d’autres réactifs. La plupart des métaux sont attaqués par les acides qui dissolvent la couche protectrice d’oxyde. L’aluminium est aussi attaqué par les solutions basiques tels que la carbonate de sodium (vendu comme soude cristallisée) qui dissolvent la couche d’oxyde. Le cas le plus spectaculaire de l’implication de l’eau est évidemment la rouille.
En l’absence de l’eau, le fer de ne semble pas s’oxyder (en fait, il y a formation d’une mince couche protectrice et plus rien ne se passe). J’ai chez moi depuis des années une boîte contenant des clous en acier qui ne montrent pas de signe d’oxydation. Le fer en contact avec l’eau sans oxygène ne s’oxyde pas non plus. Il faut la présence des trois acteurs pour que la rouille se manifeste, et le mécanisme est assez compliqué. Nous essayons de le représenter dans la Figure 3 ci-dessous. Imaginons une tige de fer trempée dans l’eau. Nous distinguons quatre zones A, B, C et D où les conditions sont assez différentes.
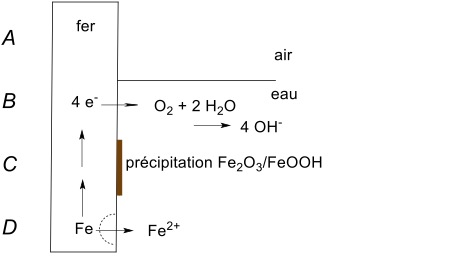
Figure 3. La corrosion du fer dans l’eau.
Dans la zone A il n’y a que le fer et l’oxygène de l’air. Il n’y a pas de réaction au-delà de la formation d’une couche protectrice d’oxyde. Dans la zone D, il n’y a pas beaucoup d’oxygène, mais le fer se dissout sous forme d’ion ferreux, Fe2+, soluble dans l’eau, et les électrons libérés par cette dissolution sont conduits par la tige métallique vers la zone B où l’eau est riche en oxygène. Dans cette zone, les électrons réagissent avec l’eau et l’oxygène pour former des ions hydroxydes, HO–. Tant que les électrons peuvent quitter la zone D, les ions Fe2+ continuent de passer dans l’eau et la corrosion se poursuit même en absence d’oxygène. Il se forme une cavité ou une piqure indiquée par la ligne pointillée dans la figure. Si vous regardez la figure 1B on voit clairement des piqures, des points où la corrosion a été particulièrement marquée.
Enfin, dans la zone C, les ions Fe2+ rencontrent des traces d’oxygène et les ions hydroxydes. Le résultat est l’oxydation des ions Fe2+ en ions ferriques, Fe3+, avec précipitation du solide rouge brun que nous associons avec la rouille, en réalité un mélange d’oxyde, Fe2O3, et d’oxohydroxyde, FeOOH. On voit que les différentes réactions chimiques sont séparées et peuvent avoir lieu dans différents endroits. Le fer peut se dissoudre dans l’eau alors qu’il n’y a pas d’oxygène dans le voisinage direct ce qui permet à la corrosion de pénétrer à l’intérieur du métal.
L’eau de mer accélère la corrosion très nettement, car les ions chlorures (provenant du chlorure de sodium, le sel, dans l’eau de mer) facilitent le passage des ions Fe2+ dans l’eau (la zone D) et accélèrent la formation des piqures, laissant la corrosion pénétrer dans le fer. Les chlorures peuvent réagir avec les couches d’oxyde (zone C) et les rendent poreuses. Enfin la corrosion peut produire la libération des protons, rendant l’eau acide et dissolvant d’éventuels couches protectrices. Un dernier effet dans l’eau de mer peut être l’activité biologique. La plupart des organismes dans la mer sont toujours à la recherche de fer et peuvent secréter des sidérophores qui captent le fer. Il a été démontré que répandre du sulfate de fer dans l’océan produit une prolifération d’algues qui n’attendaient que le fer pour pouvoir se multiplier. Dès lors ces organismes peuvent utiliser la rouille comme source de fer.
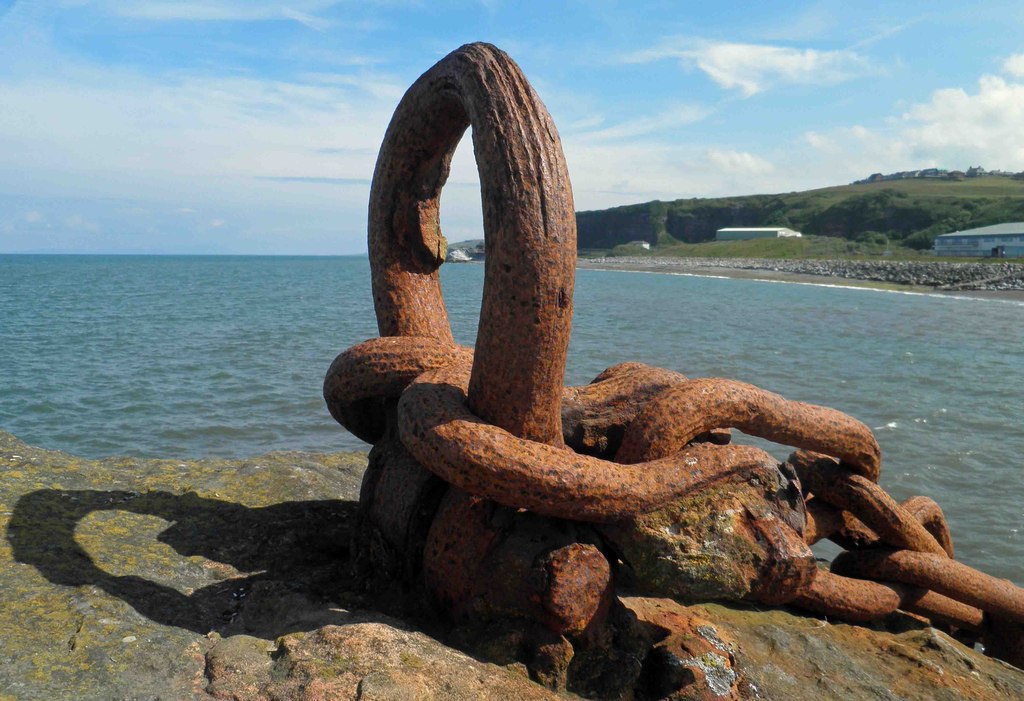
Figure 4. Une chaine en acier soumise à la corrosion par l’eau de mer. On voit clairement les fissures où l’eau salée a pénétré dans la masse. Whitehaven North Pier, Cumbria GB by Steve Fareham, CC BY-SA 2.0 <https://creativecommons.org/licenses/by-sa/2.0>, via Wikimedia Commons
Prévention et guérison
La protection
Les effets de la corrosion étant néfastes, l’homme a cherché à les prévenir voire à les diminuer. La méthode la plus simple est de mettre une couche isolante entre le métal de l’eau et l’air. Le plus souvent il s’agit d’une peinture ou d’un vernis (les cuivres étincelants d’un orchestre ou d’une fanfare sont tous protégés par un vernis). C’est efficace tant que la couche n’est pas endommagée. Une rayure permettra la corrosion de démarrer et donc les surfaces comme les grands ponts ou les bateaux sont continuellement repeintes. Pour contrôler la rouille sur de petits objets, on peut utiliser un traitement inhibiteur qui se fixe sur la couche d’oxyde et l’isole. Des dérives de l’acide phosphorique, par exemple, se lient bien à l’acier en formant une couche insoluble de phosphate ferrique.
Une méthode très efficace consiste à plaquer sur l’objet métallique une couche d’un autre métal très résistant à la corrosion, le plus souvent le chrome. Celui-ci forme une couche protectrice d’oxyde qui est résistant mécaniquement mais qui est aussi résistant à l’attaque des réactifs chimiques. Le chrome peut être déposé par une méthode électrochimique, ce qui permet de contrôler épaisseur de la couche. Quelques pas autour de votre logement (ou votre bateau) révèleront quantité d’objets chromés, particulièrement dans la salle des bains ou la robinetterie comprend typiquement des objets en laiton qui ont été chromés. La résistance du chrome lui garde un aspect argenté brillant aussi très populaire chez les motos et voitures de sport. La résistance du chrome est aussi une propriété essentielle dans l’acier inoxydable (inox), un alliage de fer qui contient au moins 10,5% de chrome (avec souvent une quantité de nickel). A la surface de l’alliage, le fer est corrodé mais laisse une couche très résistante d’oxyde de chrome ce qui donne sa résistance à la corrosion. On peut noter au passage que la présence du chrome détruit le ferromagnétisme du fer ce qui fait que les casseroles en acier inox simple ne peuvent pas être utilisées sur les cuisinières à induction.
La résistance des couches d’oxyde est aussi utilisée dans le processus d’anodisation, typiquement pour l’aluminium et le titane qui forment des oxydes très résistants. L’objet à protéger est oxydé non pas par simple exposition à l’air, mais par une oxydation électrochimique qui donne une épaisseur de couche plus grande qui résiste de ce fait bien mieux à la corrosion. L’aluminium anodisé a la particularité de pourvoir absorber des colorants, et peut donc être coloré à choix comme le montre la figure 5. Vous pourrez certainement trouver des exemples chez vous. En général, l’aluminium anodisé paraît plus mat – la plupart des objets en aluminium sont anodisés, ce que vous pouvez voir en les comparant avec une feuille d’aluminium ménager.
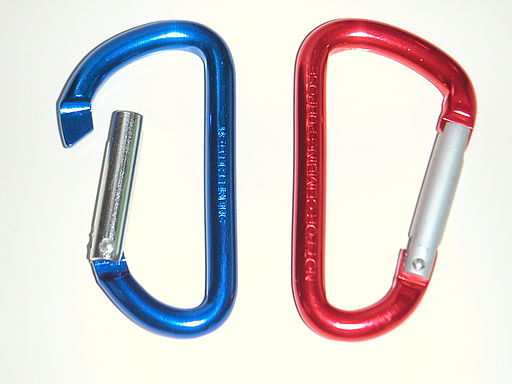
Figure 5. Deux morceaux d’aluminium anodisé où la couche d’oxyde a été colorée par l’addition de colorants. Source : Polyparadigm, public domain, via Wikimedia Commons
La réduction
Chacun sait comment le cuivre ou le laiton se ternit avec le temps. Il suffit de regarder les pièces de monnaie en cuivre pour voir comment les pièces les plus anciennes brunissent. On peut les rendre brillantes de nouveau en les polissant, ce qui consiste à enlever la couche d’oxyde. Toutefois, on peut aussi retrouver l’apparence initiale en traitant la pièce avec une solution réducteur, qui transforme la couche d’oxyde en métal. La figure 6 montre une pièce de monnaie ternie avant et après traitement avec une solution réducteur (en l’occurrence le jus de citron auquel on ajoute un peu de sucre) qui restaure la couleur rose de la pièce. En effet, on peut rendre brillants les objets en cuivre ou laiton simplement en les frottant avec un demi-citron.
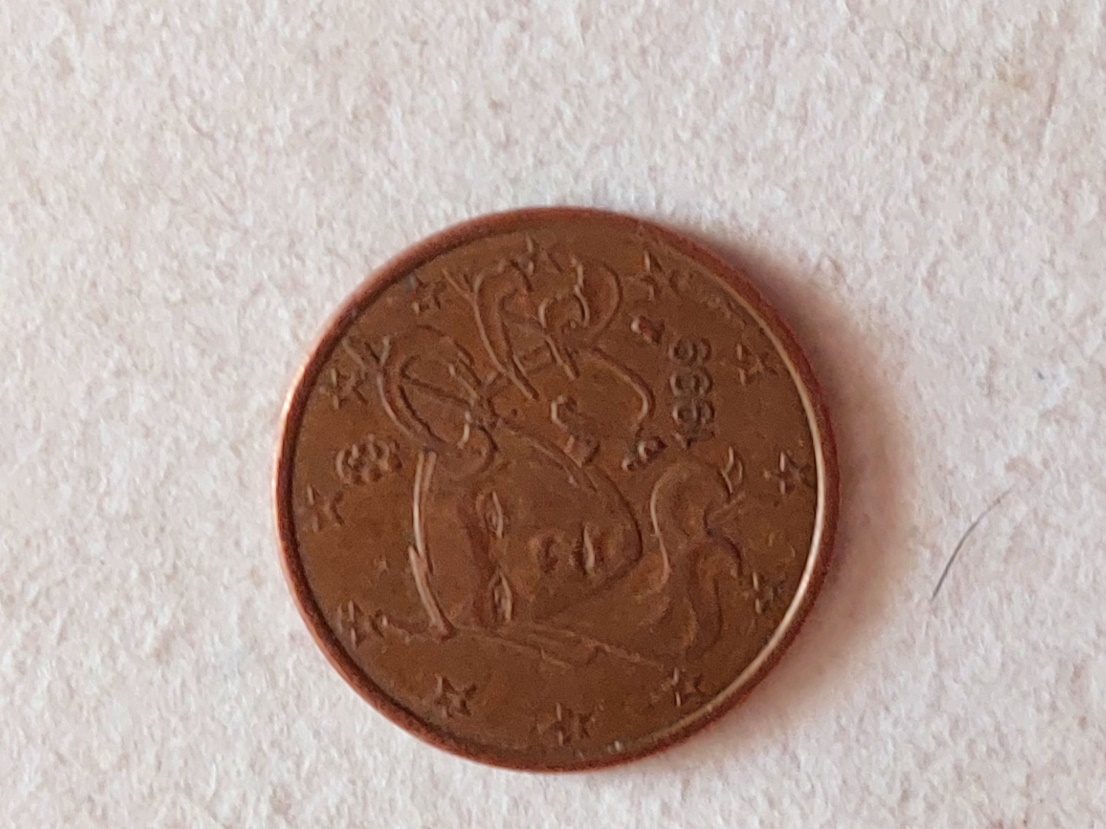
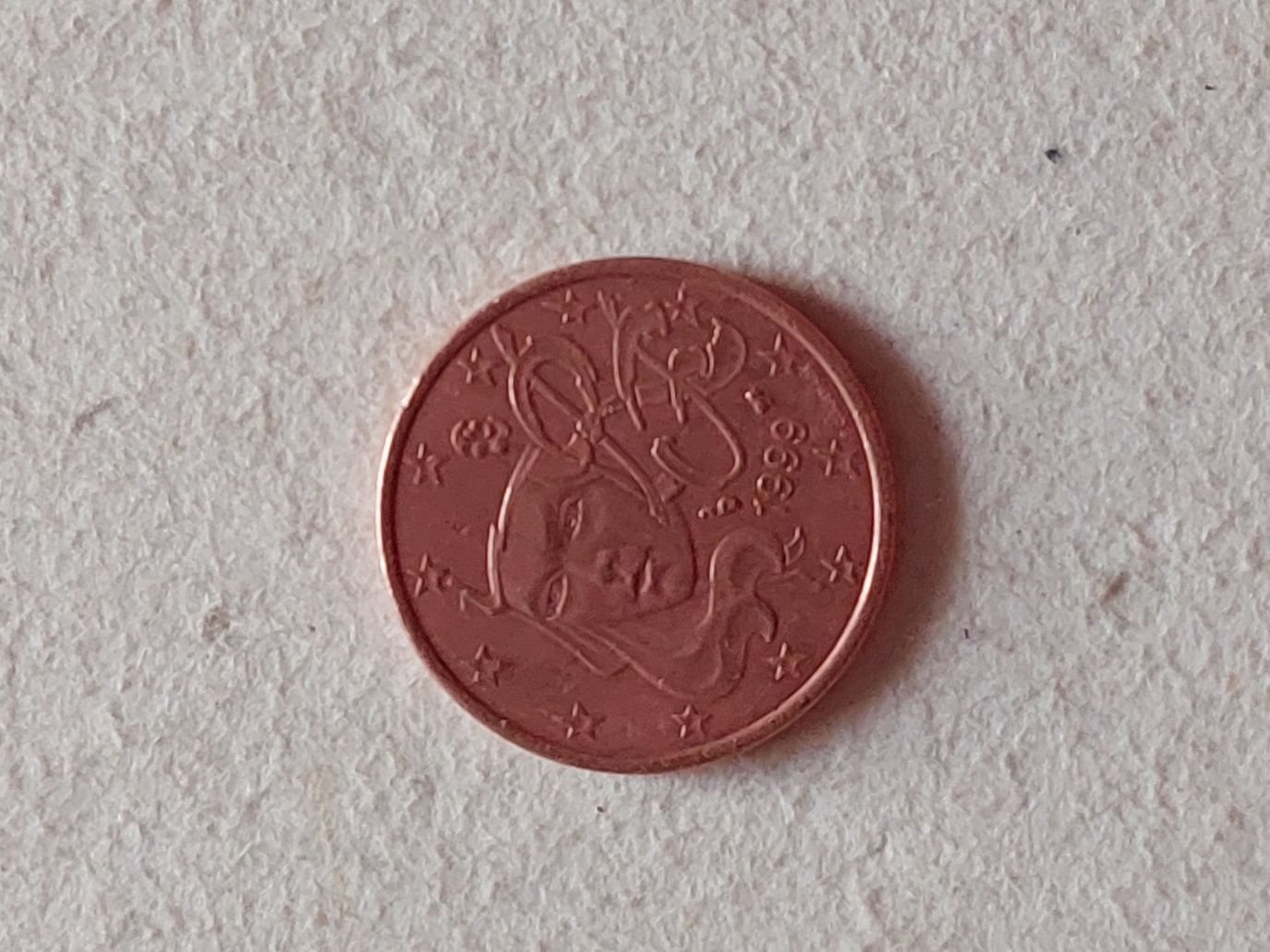
Avant Après
Figure 6. Le traitement d’une pièce avec une solution réducteur (jus de citron et sucre) restaure la couleur rose du cuivre métallique.
Les anodes sacrificielles.
Revenons enfin aux anodes mentionnées au début de cet article. Imaginons deux métaux différents en contact. Comme exemple, nous pouvons prendre le zinc et le fer (ou l’acier). Si les deux métaux sont plongés dans l’eau, chacun peut subir la corrosion, mais on peut se demander si la corrosion aura lieu à la même vitesse pour les deux. Dans ce cas précis, le zinc est plus électropositif et donc plus facilement oxydé que le fer. Le zinc se dissout en solution sous forme d’ions Zn2+ et les électrons restent sur le métal. Ces électrons peuvent traverser le métal pour réagir avec l’oxygène, mais ils peuvent aussi réagir avec d’éventuels ions Fe2+ en solution provenant de la corrosion du fer pour reformer du fer métallique. De ce fait la corrosion du fer est arrêtée, et le zinc est corrodé préférentiellement. Ceci est vrai même si le zinc ne couvre pas toute la surface du fer. Tant qu’il reste du zinc, c’est celui-ci qui sera oxydé et qui se dissoudra. Par convention, le site où l’oxydation a lieu, en notre cas le zinc, s’appelle l’anode. Puisque le zinc est corrodé à la place du fer, on l’appelle une anode sacrificielle.
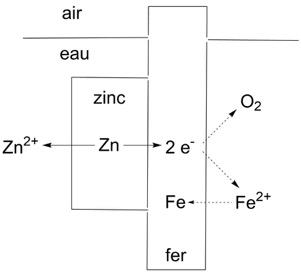
Figure 7. La galvanisation. Le zinc en contact avec le fer est oxydé en Zn2+ et les électrons passent à travers le métal vers le fer où ils peuvent réagir avec l’oxygène ou réduire du fer oxydé (Fe2+) en fer métallique. Si le zinc est exposé à l’air il se forme une couche d’oxyde de zinc ZnO.
Notre choix de zinc et du fer comme métaux n’a rien d’accidentel, car c’est la base de la technique de galvanisation, après le physicien et médecin Italien Luigi Galvani, qui consiste recouvrir un objet en fer ou acier d’une mince couche de zinc. Le zinc a plusieurs avantages : c’est un métal relativement bon marché, non-toxique, qui fond à seulement 420°C. Il est donc facile de protéger les objets en fer en les plongeant brièvement dans un bain de zinc fondu, quoique d’autres méthodes de traitement comme le plaquage électrochimique puissent être utilisées. Un objet fraîchement galvanisé a une allure gris-argentée, mais avec le temps, le zinc s’oxyde et l’objet paraît gris. Une bonne galvanisation peut résister à la corrosion pendant des dizaines d’années sans intervention. Une fois le zinc tout oxydé toutefois, la corrosion reprendra ses droits ! La figure 7 montre un grillage qui a deux parties : le plus ancien, en bas, a perdu tout son zinc et la rouille avance, avec la formation des piqures ; la partie supérieure, plus récente, a encore la couche de zinc quoique la perte de brillance montre qu’une couche d’oxyde s’est formée. Les objets galvanisés sont partout – pendant la préparation de cet article j’avais l’occasion d’attendre un train, et sur le quai j’ai noté que les lampadaires, les pylônes qui supportaient le catenaire, le grillage qui séparait le chemin de fer de la route et les glissières de sécurité de la route étaient tous galvanisés.
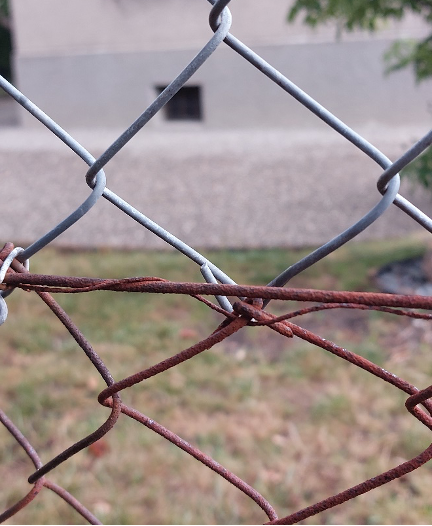
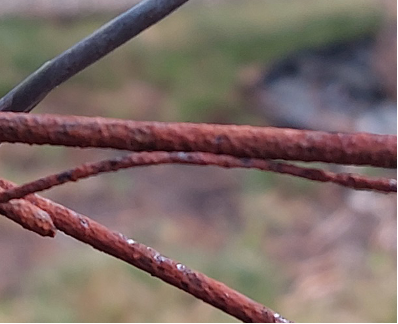
Figure 7. Un grillage avec deux parties, une nouvelle et l’autre ancienne. Sur la nouvelle (en haut), le zinc protège le fer et on voit une couche d’oxyde de zinc. Sur le grillage ancien, le zinc est parti et le fer commence à rouiller. Dans l’agrandissement, en bas, ou peut voir la surface rugueuse du fer rouillé due à la formation de petites piqures.
Si le couple zinc/fer est le plus courant, en principe toute combinaison d’un métal électropositif et d’un métal moins électropositif peut montrer cet effet. Les anodes sacrificielles, c’est à dire les métaux électropositifs qui s’oxydent préférentiellement, peuvent être en zinc mais aussi aluminium. Le métal protégé est le plus souvent le fer, mais dans le cas de Gaia, il s’agit du bronze de l’hélice. La seule condition est que les électrons de l’anode puissent passer au métal à protéger. Une amie à découvert ceci de manière involontaire : en voulant proposer à ses invités du jambon de Parme, elle a déposé le jambon sur un beau plat en argent, puis, ne voulant pas que la viande s’assèche, l’a recouverte d’une feuille d’aluminium. Vous aurez, j’espère, reconnu la combinaison d’un métal électropositif (l’aluminium) et un moins électropositif (l’argent). Une heure plus tard, l’aluminium s’est oxydé, la feuille était trouée, et le jambon, imbibé d’ions Al3+, était immangeable. La corrosion peut se présenter là où l’on l’attend le moins.